BIG TANKS
Download more information about Infratank tanks. Strength, performance, quality, longevity and exceptional durability.
- Request a Quote
- Call us: 09 869 3030
- Email: [email protected]
- Office: 3 Averton Place East Tamaki Auckland 2013
Volumes
Infrapipe can offer the following volumes for example but it is important to note that as tanks can be seamlessly joined on site – in any dimension, orientation or angle – then any volume can be created. Here are some typical configurations:
DIAMETER | 6m | 12m | 18m | 30m | 50m |
1500mm | 11m3 | 21m3 | 32m3 | 53m3 | 88m3 |
1800mm | 15m3 | 31m3 | 46m3 | 76m3 | 127m3 |
2000mm | 19m3 | 38m3 | 57m3 | 94m3 | 157m3 |
2500mm | 29m3 | 59m3 | 88m3 | 147m3 | 245m3 |
3200mm | 48m3 | 96m3 | 145m3 | 241m3 | 402m3 |
3500mm | 173m3 | 288m3 | 481m3 |
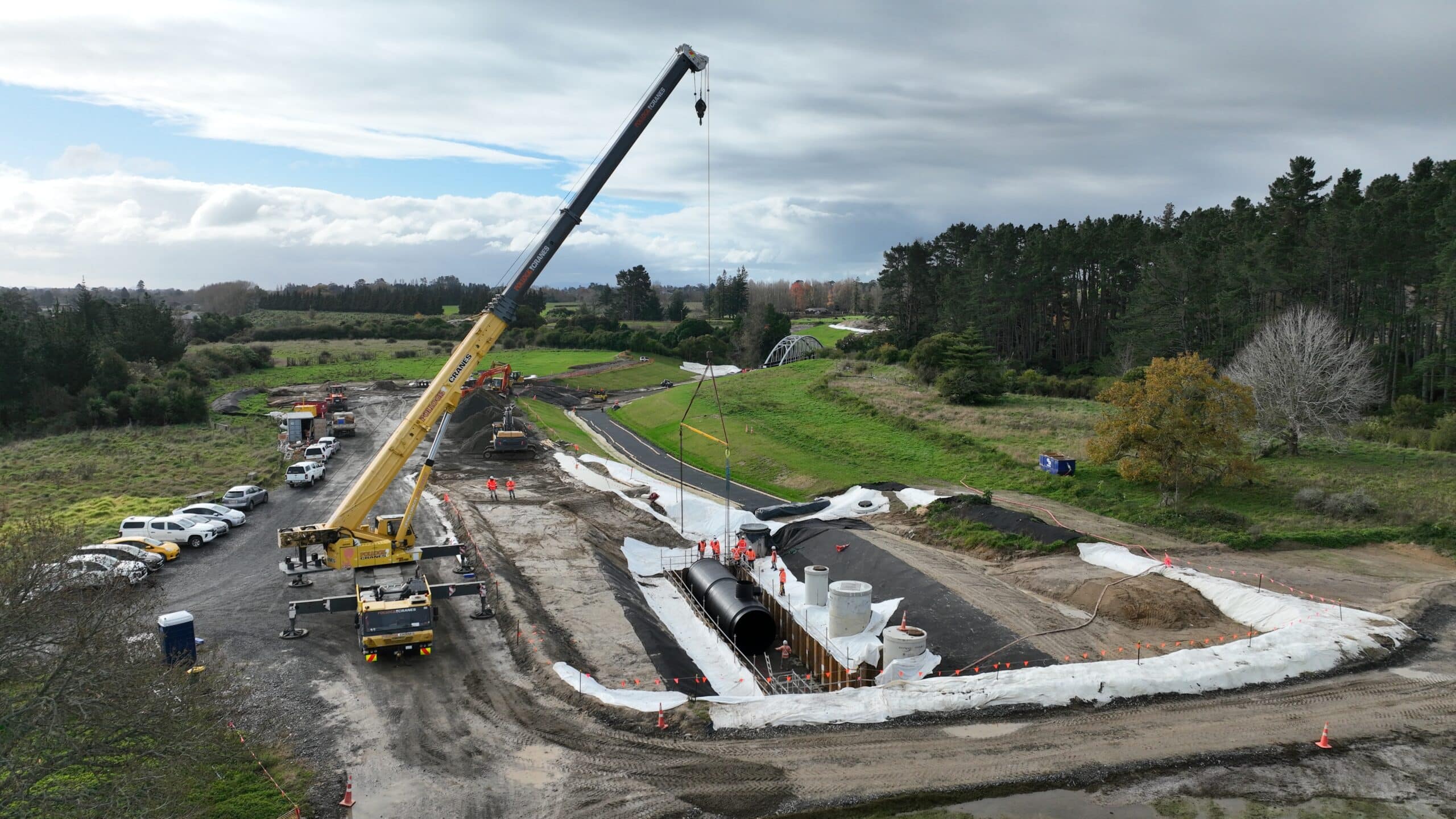
Benefits
HDPE tanks have a 100 year life and the following benefits:
- Lighter
- The best abrasion resistance.
- The best seismic resistance.
- The best chemical resistance.
- The best biological resistance.
- The best damage resistance
- No maintenance.
- Lowest overall cost.
- Long life 100 yrs+
- Completely recyclable.
- Very flexible design.
- Any risers possible.
- Short leadtime.
- Easy to install.
- Safer to work with.
- Easy to modify.
- Best for the environment.
- Made in New Zealand.
This page is for tanks for stormwater, wastewater, potable water, fire fighting or other applications.
- For small diameter stormwater see DRAINAGE.
- For small rural culverts see SMALL CULVERTS.
- For wastewater applications see WASTE WATER.
- For large culverts, see ENGINEERED LARGE CULVERT.
- To go direct to the Stormwater Design Manual or Datasheets for INFRAPIPE KRAH, CIVILPIPE or MANHOLES go to the Downloads page.
What standards does Infratank comply with?
Infrapipe has AS/NZS 5065:2005 certification and ISO 9001:2015. Calculations are in accordance with AS/NZS 2566.1:1998 – Buried Flexible pipelines: Structural Design. Design and installation parameters used are in accordance with AS/NZS 2566.2:2002 – Buried flexible pipelines – Installation
Design Options – main vessel
The base module of the Infratank, an HDPE pipe 6m long, can be cut and welded in any way possible to form any shape. This allows the designer to optimize the solution for the site, for economic installation, for economic operation thereafter and for future modification.
Some options shown below show how this flexible system can be used, but we stress the importance of early discussions with Infrapipe to realise the potential of the product and the site:
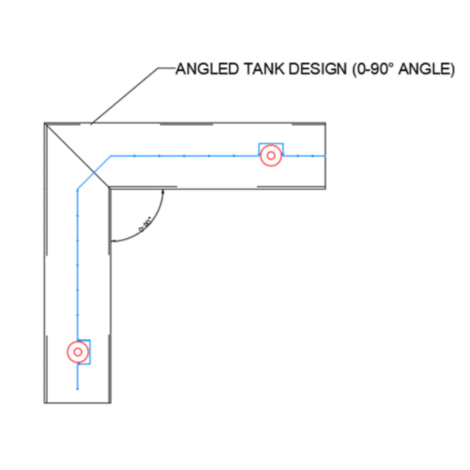
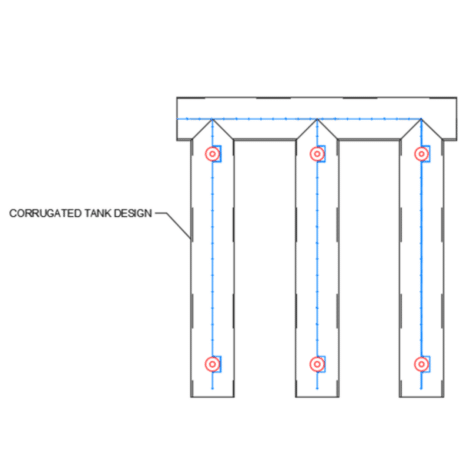
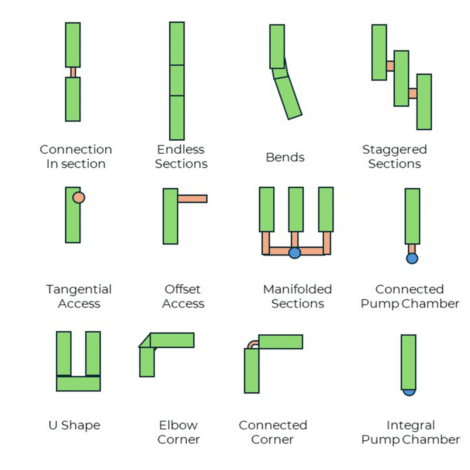
Above ground tanks
The use of helical HDPE for above ground tanks is common overseas and has the same flexibility of design for connections. Contact [email protected] for more details.
Vertical tanks used a stepped profile to save material and weight, increasing the ring stiffness lower in the cylinder.
What is an offset access?
The flexible construction of an Infratank allows for an inspection access which is offset from the tank itself, allowing tanks to be placed under roads or in other locations where frequent access to the riser for inspection is expensive, inefficient or unsafe.
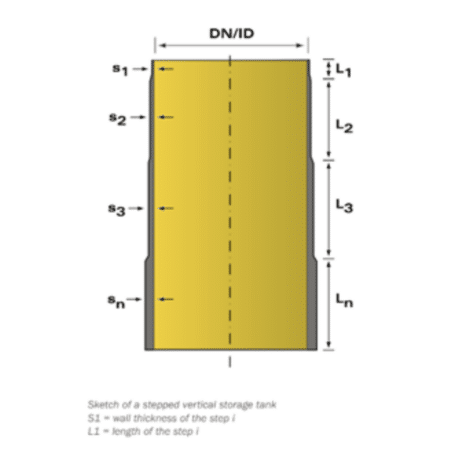

The scope of tank supply
- From the perspective of the designer, the contractor or the asset manager, the tank is a subsystem which is supplied by Infrapipe. If the tank subsystem is effectively a black box in the drawings (where the designer is responsible for designing everything up to and around the box but relying on the supplier for the box itself), the lists below explain what is in the box, what connects to the box and what is not in the box but is affected by it. Infrapipe therefore defines:
Standard Items supplied by Infrapipe
ITEMS | DETAILS |
Inlets | As required to the bare flange, typical stub is 500mm |
Outlets | As required to the bare flange, typical stub is 500mm |
Sumps | Any depth as required to a diameter not more than 500mm greater than the tank diameter |
Risers | Any height as required to a diameter not more than 500mm greater than the tank diameter |
Ladder steps | PE/PP steps every 300mm for access |
Lid | Concrete manhole lid as per design on load distribution ring |
Cover | As specified by client or determined by INF structural calculations |
Hydrophilic seal | Placed around the neck of riser fully covered in copolymer foam |
Loadring | As per structural design |
Low flow chambers | Flow management and sediment control as per client specification |
Baffles | HDPE baffles installed by INF fabricators as per client specification |
Buoyancy anchors | Either INFRAPIPE standard anchors or if the contractor prefers, a design so they can pour their own |
Anchor straps | Straps as required for the anchor system |
Subsystems supplied by Infrapipe
Washdown System
- INFRAPIPE works with third party suppliers to provide a washdown system fitted and connected to the exterior inlet and outlet. The scope concludes at the bare flange 500mm from the tank but the design will include the required water volume to operate the system. Systems can be either HDPE or stainless steel.
Pump system
- Infrapipe works with third party suppliers to integrate pump systems into the tank. Initial quotes use nationwide options but if end-users have preferred pump models the design can be modified in later stages to accommodate them. The scope concludes at the power supply to the pump.
Items not supplied by Infrapipe but for which data can be provided
To assist the designer, the quantity surveyor and contractors, Infrapipe details the following products and services required to install or support the tank
ITEMS | DETAILS |
Water supply to the washdown | Number and size of inlets and outlets and required litres/second is specified by Infrapipe |
Power supply for pump | Power supply specified by pump supplier as per washdown system needs |
Excavation m3 | For standard soils & cover until geotechnical info provided |
Backfill m3 | For standard soils & cover until geotechnical info provided |
Sheet pile/shields | Based on trench size |
Craneage weights at distance | Lift plan to be supplied by crane operator according to site access and tank weight |
Craneage hours | A prediction of crane hours on site for both time management and costing of installation |
Scaffolding for testing | Specification from INF staff on what scaffolding is needed to ensure safe entry into tank for on site works. |
Installation timeline | A prediction for the calculation of related costs. |
Items not supplied but which are relevant to the tank supply
ITEMS | DETAILS |
Sensors | Level sensors to ensure safe & efficient operation of the tank. |
Controls for washdown water supply and housing | Backflow preventors, flow control valves, pressure regulators and other controls to ensure efficiency of washdown as well as safety of the water supply. |
Housing for pump control | Protective enclosure to ensure safety of both equipment and personnel. |
Gaskets for flanges | Typically EPDM Gaskets for watertightness between flanges. |
Connection to the inlet and outlet | Flanged, coupled or welded connection between tank stubs and external inlet/outlets. |
Installation and test plan
Infrapipe will supply an Installation and Test Plan which details contractor requirements at each stage:
- Receiving the pipes
- Laying the pipes
- Joining the pipes
- Testing the tank
- Joining connections
- Completing the tank
Trench specifications
Infrapipe will specify the trench dimensions and materials for each of the following stages:
- Laying and joining
- Testing
- Completion
Drawing of tank in plan and profile showing extent of scope (red border)
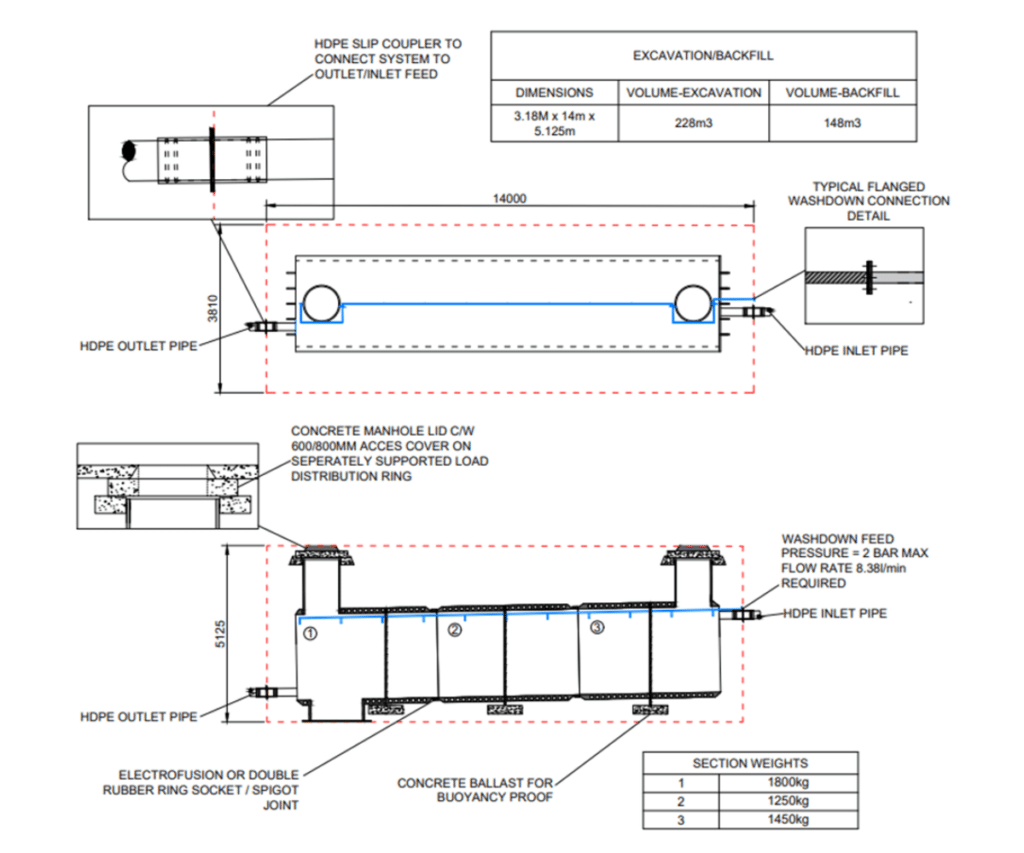
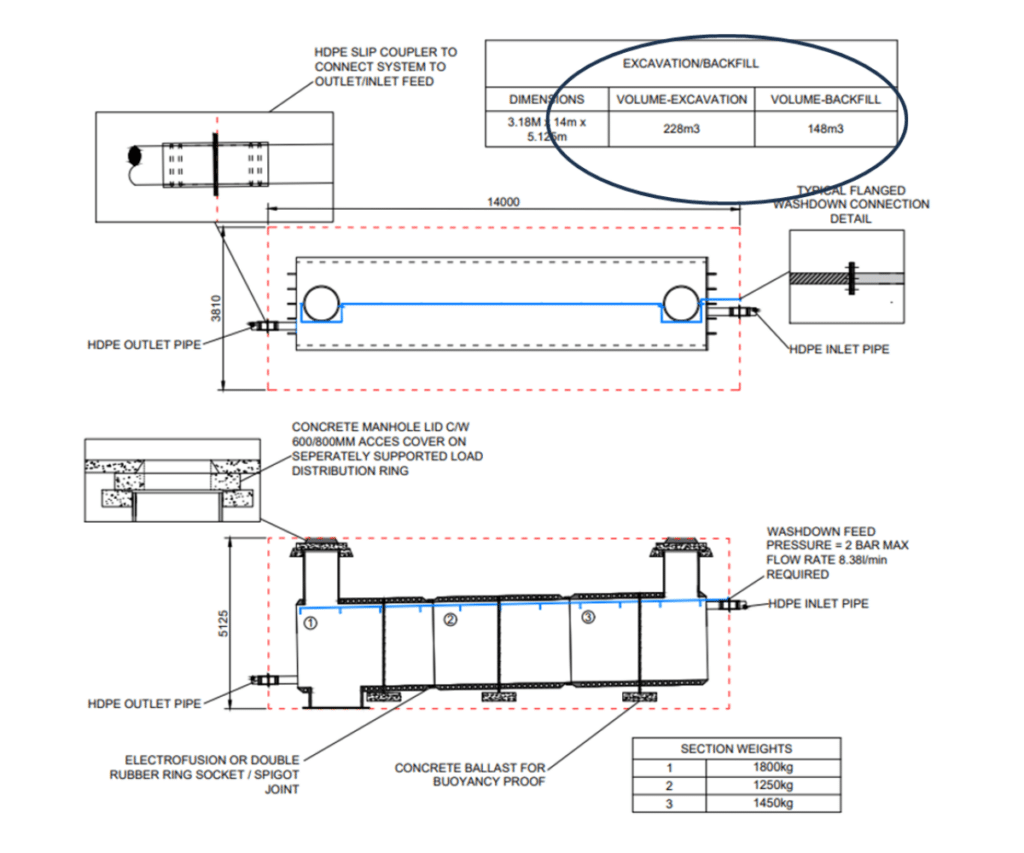
How are sections joined?
Once located and aligned, Infratank sections are joined with one of two methods:
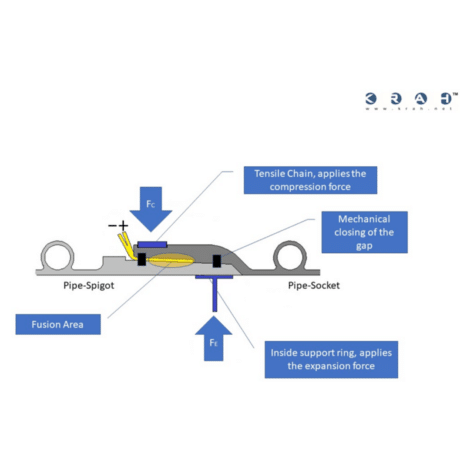
- The first, electrofusion, uses the 30% expansion of HDPE 100 when heated to 135 degrees to bond the two surfaces completely in a process that takes two staff (normally INFRAPIPE staff) approximately 45 minutes.
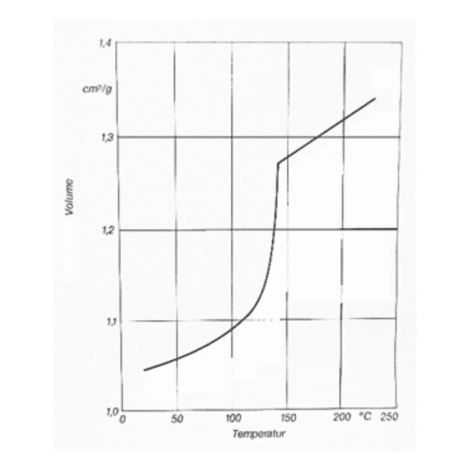
- The other alternative is a double rubber ring joint as shown below.
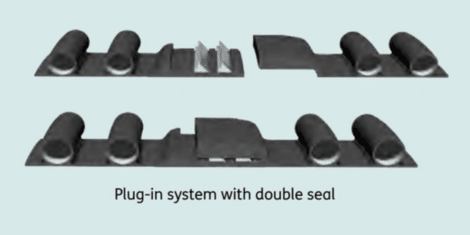
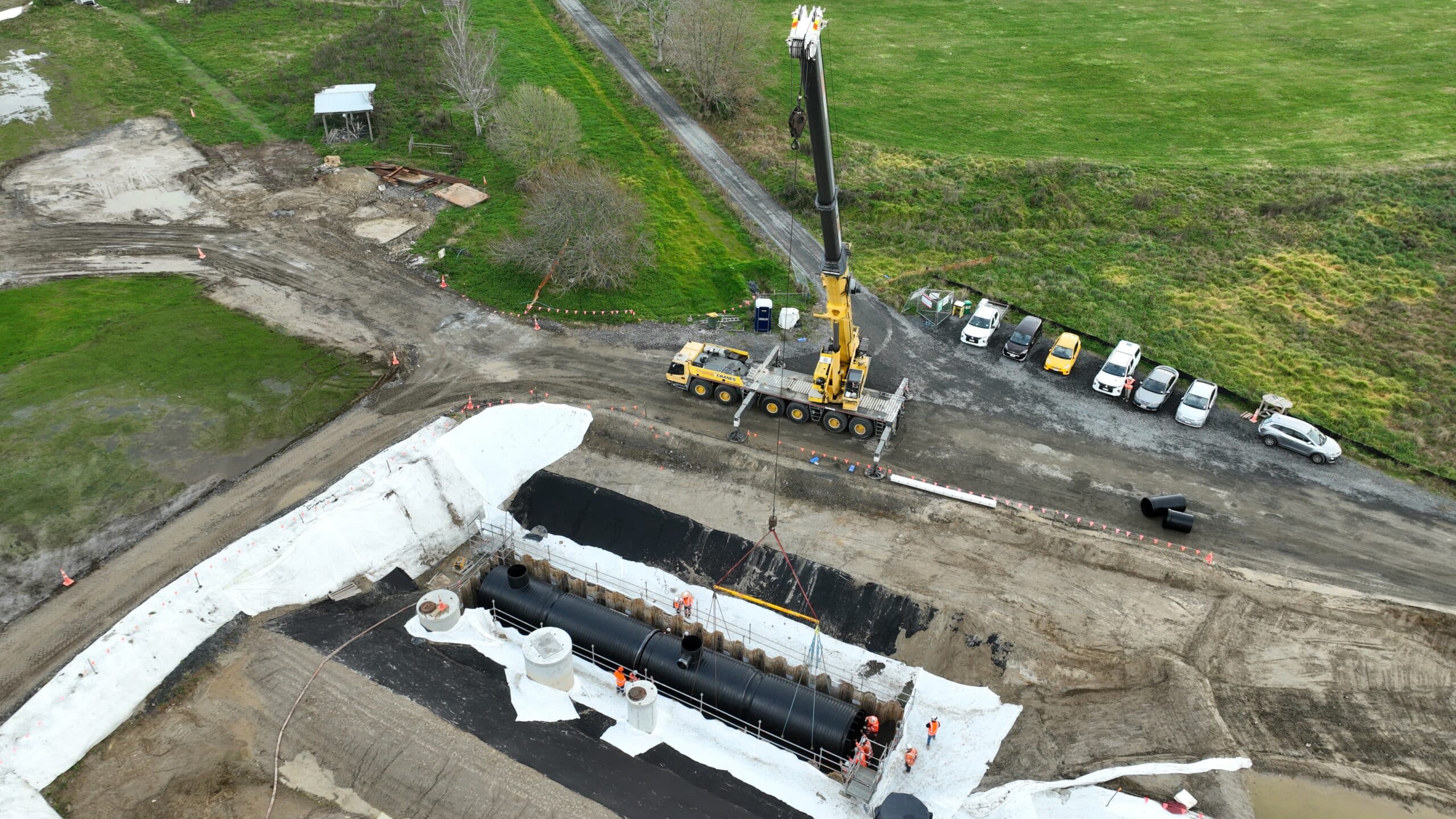
Design Process
Infrapipe will engage at every stage of the process to ensure that the appropriate professional has all the information required:
Initial Scheme Design
Potential options and provisional costings to optimise use of the site and hydraulic efficiency and minimize manufacture, freight and installation costs.
Engineers Estimate
At this stage Infrapipe can supply an estimate without geotechnical information or invert levels:
1) Basic design including the location of
a. Inlets
b. Outlets
c. Risers
d. Accessways
e. Sumps
2) Delivered to site system estimate including
a. Washdown system
b. Pump system
c. Freight
3) Installation costs estimate
4) Requirements for other services (washdown and pump)
5) Installation requirements
Contractors quote
At this stage a Geotech report, site design, invert levels, gradients and confirmation of the hydraulic design is essential. Cover to be determined by either Contractor specification or INF structural calculations. Infrapipe will supply:
- Full tank design
- Manufactured and delivered cost
- Requirements for other services (washdown and pump)
- Installation requirements as per structural calculation
At this stage INFRAPIPE can confirm with the contractor if they wish to supply buoyancy anchors and straps, loadrings, lids and access covers.
Contract accepted
Once the quote is accepted, variations can typically be made without penalty cost up to two weeks before delivery (exact dates to be confirmed during quotation). The following is provided:
- Installation and Test Plan
- Fabricated products installation guide
- Final drawings
Final Documentation
Following completion and successful testing, Infrapipe will supply the following:
- Maintenance instructions for the washdown system.
- Pump maintenance instructions.
- Quality assurance for tank and fabrication.
There are no maintenance requirements for the tank structure.
Installation Process
- Site preparation
- Excavation
- Install sheet piles/shields
- Base preparation
- Bring in connections
- Prep ground
- Lay section, join and weld (repeat as necessary)
- Backfill to spring line
- Test
- Complete connections
- Backfill
- Compact
- Completion of pump, sensors etc.
- Site restitution
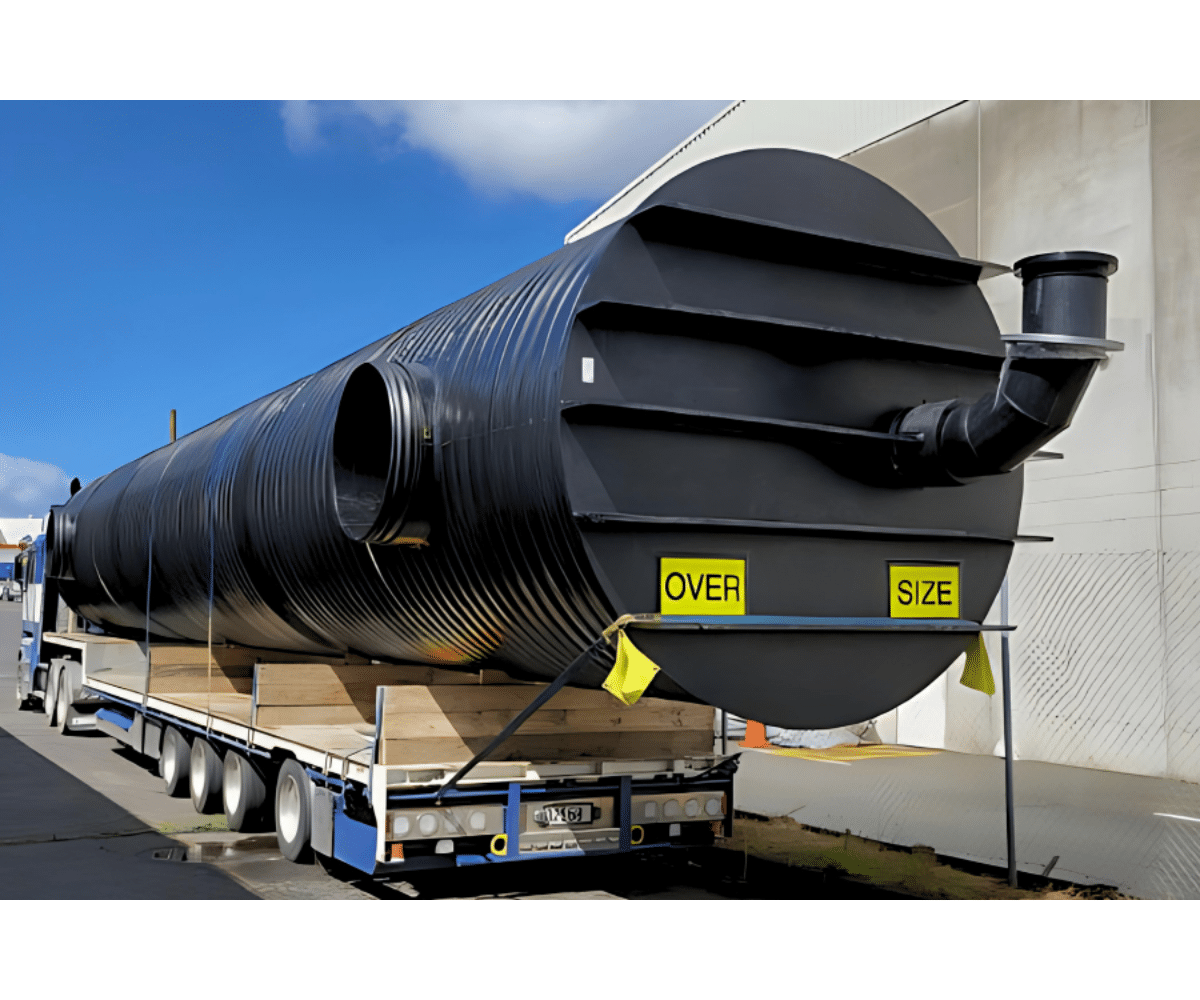
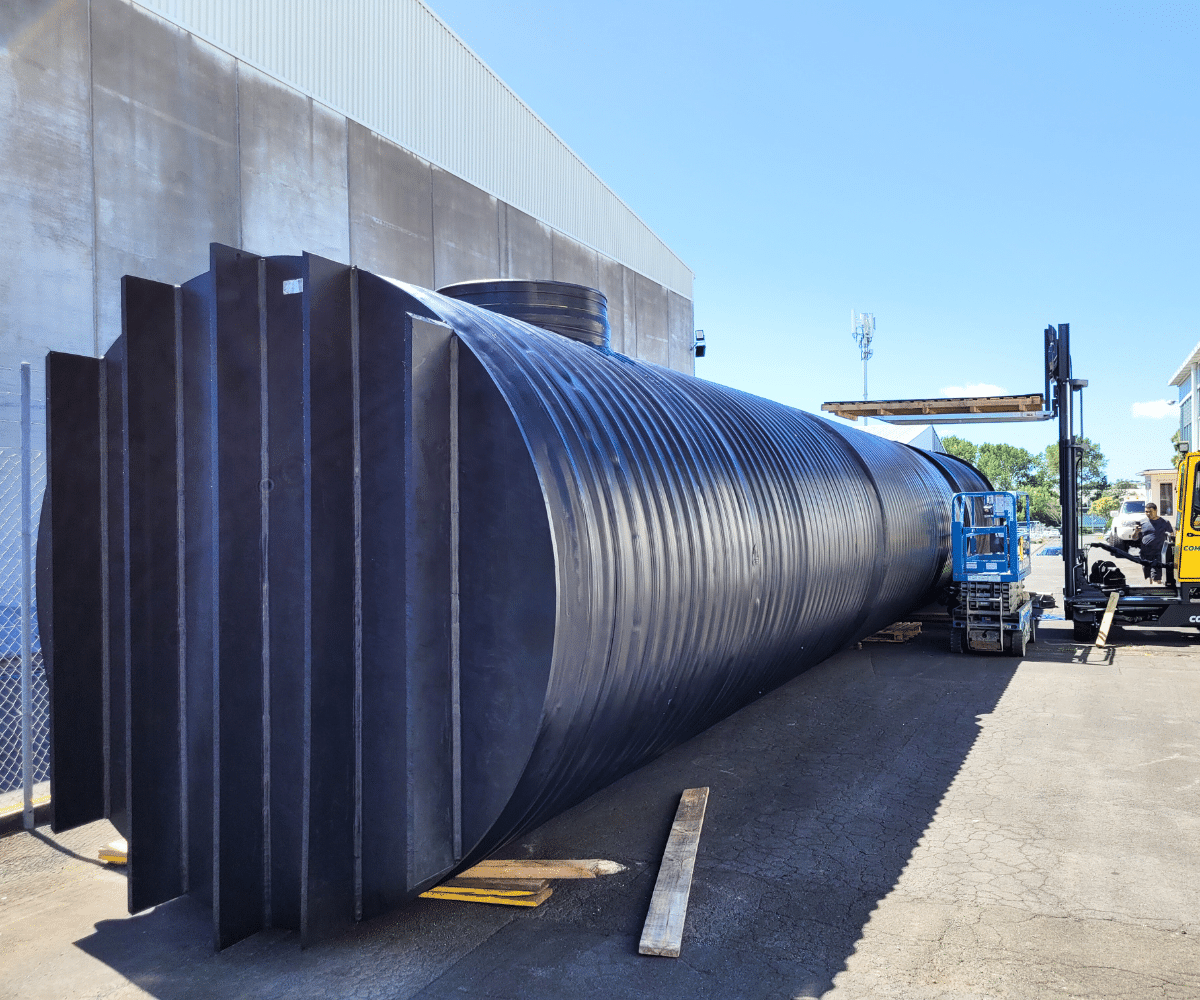
FAQs
These are some of the questions most commonly asked about Infratank:
How do we know it will last one hundred years?
Products of this kind have been in use in Germany since 1956 and continuously tested since then without any degradation:
What is the leadtime?
For tanks up to 200m3, leadtime is 2-4 weeks. For applications over this size, typical leadtime is 4-6 weeks except by arrangement.
Bespoke layouts & configuration may differ from standard lead times.
What is Infrapipe’s production capacity?
We can make and weld at least 3 large diameter pipes each working day, so maximum capacity ranges from 108 lineal metres per week of 3.2m pipe to approx. 180 lineal metres per week of 2.3m pipe.
How does Infratank address buoyancy?
Infrapipe’s civil engineers will calculate the buoyancy potential once they have the relevant geotechnical information and water table levels. Infrapipe will then offer to provide and install the required numbers of its anchors, or will provide the requirements for the alternative option of site poured slab(s) underneath.
How do Infratanks handle seismic events?
HDPE pipes have high flexibility allowing them to absorb seismic energy without breaking or cracking. The ductile nature of PE allows the pipe to deform without breaking, allowing them to stretch and elongate rather than fracture. Fusion welding is used to join the pipes together to create a bond as strong as, if not stronger than the pipe itself ensuring the joints do not break or leak during a seismic event.
What happens if the tank is damaged
It is not easy to damage HDPE but should this occur (before, during or after installation), Infrapipe’s site services team can repair with welding onsite.
If the tank is damaged in subsequent years, any qualified HDPE welder can repair the tank quickly and easily with welding being dry and usable within 45 minutes of completion. HDPE is homogeneous (ie it has no need of a protective gelcoat or paint) so damage is easy to deal with and has no impact on longevity.
Can the tank be modified?
Should there be a future requirement to modify the tank, with additional connections for instance, this can be conducted on site quickly and easily by Infrapipe’s team, giving asset managers the flexibility to consider further options
What maintenance is required?
Infratanks require no maintenance on the body of the tank. Ever. There is no rotting, rusting or corroding. HDPE is completely unaffected by any NZ soil.
Can the tank be recycled?
Infratanks are completely recyclable. All production waste is recycled into culvert.
What is the carbon footprint?
Whilst each application varies (due to location and design), HDPE generally has an environmental cost of 1.92 CE/kg and when it is then recycled this drops to 0.23 CE/kg.
About INFRAPIPE
- Infrapipe is an NZ-owned business with factories in Auckland and Palmerston North. It was established to offer New Zealand the latest pipe technologies which are now standard in the Northern hemisphere.